How We DIYed our Brass Shower Door
- Alyssa Wieske
- Jul 9, 2020
- 4 min read
Updated: Jan 10, 2024
A few weeks ago, we shared the reveal for our ORC bedroom makeover (you can see the full post here!) and one of the details I was most excited about was the shower door. For the last few years, I’ve been pinning glass shower doors with either a black or brass frame. I love the custom look and detail they add to a standard glass shower door, however to have one made was outside of what we were looking to spend. I searched all over google to see if someone had been able to pull of a DIY, but wasn’t able to find anything. I still wasn’t quite able to give up on the idea, and after talking it over with Steve, we came up with a bit of a plan and just decided to go for it. I’m not going to lie, I was a little nervous with how it would turn out and if it would even work. (It’s always a bit reassuring to see someone tackle something similar before diving in!) We did have to pivot a bit on the way, but all in all it turned out better than I could of asked. After sharing the reveal, it turned out you guys loved the look just as much as I did, and wanted to see how we were able to pull it off. So here is a bit of a tutorial post along with the progress images.
SUPPLY LIST
Here’s what we used:
-Glass shower doorÂ
-Two Unlaquered brass egg knobs (we went with the larger size)
-1/8″ thick brass sheets cut to 3/4″ width strips – We were able to use a local supplier who was able to cut the brass to size for us
-Two 10″ x 4″ brass plates 1/8″ thick
-Stir stick
-Measuring tape
–Razor blade
-Grinder
-Drill
–Clamps
STEP ONE
After getting the shower door hung with the antique brass hinges, the next step was mapping out the design. I used painters tape to draw out the frame, grids, and plate sizes. It helped me picture how the finished door would look, and also gave us an idea of how much brass we would need.
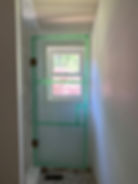
STEP TWO
With the design taped out, we were able to measure the sizes for the brass. For the two plates, we went with 4″W x 10″H x 1/8″D. The brass strips to make up the frame were 3/4″W and 1/8″ thick. We measured to have the vertical pieces on the left and right side of the door to run the full length of the door, and have the horizontal pieces run into them. When measuring the lengths of each strip, we added on a couple extra inches so that each piece could be cut down to size onsite. We also planned the brass frame to finish just above the waterproof strip along the bottom of the door.

STEP THREE
Once we had the sizes for each piece, we were able to purchase the brass from a local supplier, and have it cut to size. We also got a few extra small pieces to test out the brass aging solution on. We noticed that some of the pieces had a bit of a curve, so before starting we twisted them to get each strip as straight as possible. We also sanded down the edges of each strip with a sanding wheel on a grinder to get rid of any sharp edges, and allow the brass to sit flush on the glass. The flatter the brass sits on the door, the better the adhesive will work.

STEP FOUR
We remeasured the pieces that would make up the full height of the left and right side of the door, and cut them down to the exact size with the grinder.
STEP FIVE
With some supplies from around our home, we were able to make a long trough that was just a bit taller than the shower door. We lined it with a plastic sheet, and filled it with the aging solution and water, according to the directions.

STEP FIVE
Now that the solution was ready, we were ready to age the first pieces. Using a glove, we lifted the pieces out of the solution to keep an eye on the colouring. We found that two minutes was perfect for our pieces. Just one thing to note is that they will keep aging a bit AFTER you remove them from the solution.
STEP SIX
Once they had dried, we use the two part epoxy from JB Weld to fasten them to the glass, and used clamps to hold them in place until they were secured.

STEP SEVEN
After we had the left and right vertical pieces in place, we were able to get the exact measurements for the cross sections, cut them down to size and put them in the aging solution. Some of the brass strips didn’t allow us to use the clamps, so we found it worked best to physically hold them in place for a few minutes as the JB Weld dried.

STEP EIGHT
And finally we were able to age the door handle plates and knobs in the solution, and install them. We had a predrilled hole in the glass, and made a hole to match on the two brass plates. After the plates were fastened to the glass, we were able to thread two of the egg knobs into each other.
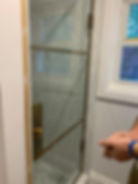
STEP NINE
And as a final step, we used a razor to the lift some of the excess epoxy off the glass.

There you have it! That is a full look at how we made the brass frame. It’s easier than you might think, as long as you are able to measure accurately. Let me know if you have any questions in the comments below, and I’d love to see photos if anyone else decides to tackle this project.